Da das Erz nur in seltenen Fällen so rein in der Grube gewonnen wurde, dass es sofort zur Hütte geliefert werden konnte, mußte es aufbereitet werden. Die erste der beginnenden Aufbereitungsarbeiten war das Ausschlagen der Erze. Ausschlagen nennt der Bergmann die erste rohe Trennung des Erzes von anhängenden Ganggestein. Das gereinigte und sortierte Erz wurde auf einen Haufen gestürzt.
Aufbereitung des Erzes
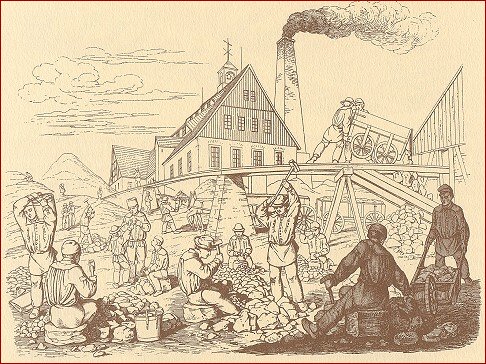
Das geförderte Erz ist zum Schmelzen nicht tauglich, erst durch die Aufbereitung wird es verhüttungsfähig. Die Erze treten selten rein auf. Größtenteils sind sie miteinander und mit Gangarten verwaschen.
Bei grober Verwaschung war das Scheiden von Hand und Aussortieren ein wichtiger Arbeitsschritt. Dazu wurden Scheidebänke eingerichtet. Sie bestanden aus grob gezimmerten Holztafeln und traten meist in Gestalt von größeren Gebäuden oder Hallen in Erscheinung, welche sehr viele große Fenster besaßen, um möglichst viel Tageslicht zum Scheiden der Minerale zu nutzen.
Dort wurden sie auf die Bühne gebracht und daselbst auf Scheideörtern (in die Scheidebühne eingesetzten Platten) in verschiedene Produkte (Bleiglanz, Bleierz, kiesiges und spatiges Dürrerz, Scheidemehl und Grubenklein) geschieden.
Enthielt ein Kübel besonders gute Erzgänge, so wurde er zuerst zum Huthaus in die Beamtenstube gebracht, erst dann zur Scheidebank.
An der Scheidebank arbeiteten ausschließlich Kinder und Berginvaliden. Die 8- bis 16-jährigen Kinder wurden als Scheidejungen bezeichnet und arbeiteten in Gruppen von 50 bis 60 Jungen zugleich unter der Aufsicht des Scheidesteigers.
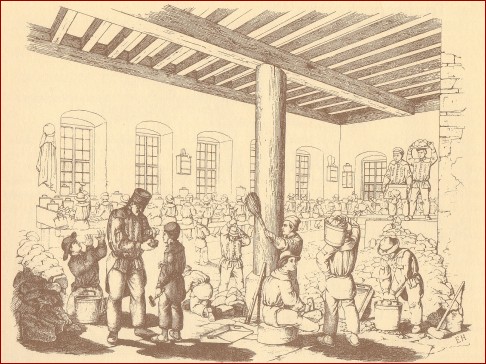
Nun schied sich die weiter Aufbereitung in die nasse oder trockene Methode.
Dasjenige Erz, was schon in kleineren Stücken und mit Schmutz aus der Grube gefördert wurde, Grubenklein genannt, mußte ehe es weiter zerkleinert werden konnte, gewaschen werden. Dies geschah durch die Abläutermaschine.Das Erz wurde in die Rollen gestürzt, welche sich über der Maschine befanden. Anschließend wurde das Grubenklein in ein Sieb geschüttet und gewaschen.Das Sieb wurde danach im Wasser geschwenkt bis die Erzstücke rein abgespült waren. Danach wurden die Stücke nach verschiedenen Größen sortiert.
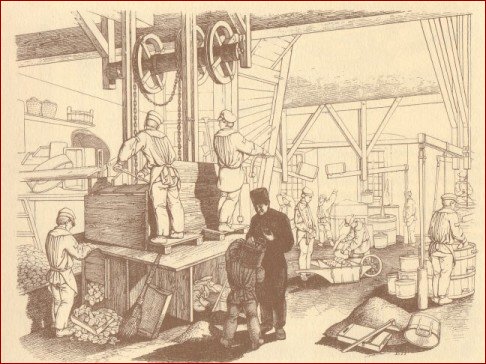
Fein verwaschenes Erz wurde im Nasspochwerk zerkleinert. Durch eine wasserradgetriebene Pochwelle wurden die etwa 3 Meter hohen und 135 kg schweren Pochstempel gehoben und zerstampften beim Niederfallen das untergelegte Pochgut. Dieses fiel aus einer Rolle in den Pochkasten. Duch Zusetzen von Wasser erhielt man einen Erzschlamm. Dieser wurde anschließend auf die Stoßherde gebracht.
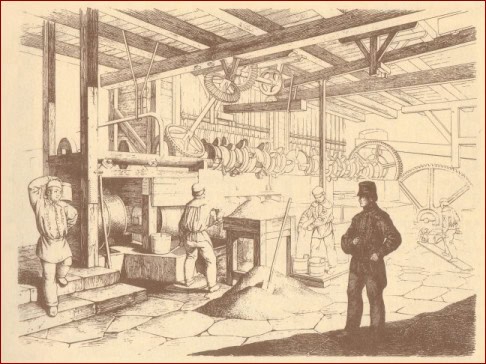
Der Stoßherd bestand aus einer großen hölzeren Tafel, welche an der Vorderseite offen und an den übrigen mit einer Borde verschlossen war. Diese war an Ketten so aufgehangen, das sie durch einen Stoß von hinten nach vorn geschoben wurde um durch eine gewaltige Erschütterung wieder an die Rückseite anzuschlagen. Das Wasser spülte die leichten Teile weg, das schwere Erz wurde entnommen.
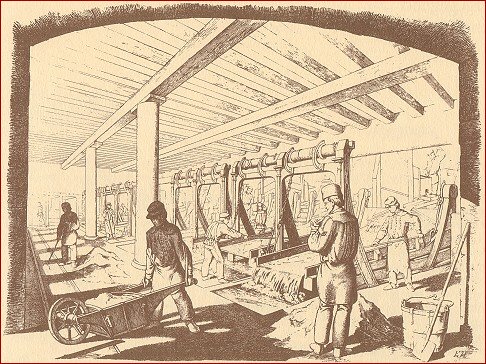
Neben Erzen, die gleich zur Hütte gebracht wurden, gab es noch das oben erwähnte Grubenklein, welches ins Trockenpochwerk beziehungsweise Walz- oder Quetschwerk gebracht wurde. Im Trockenpochwerk, das aus einer Reihe schwerer hölzerner Stempel bestand, welche am unteren Ende mit dem 40 bis 60 kg Pocheisen versehen waren, wurden die Erze bis zu Mehlstaub zerkleinert.
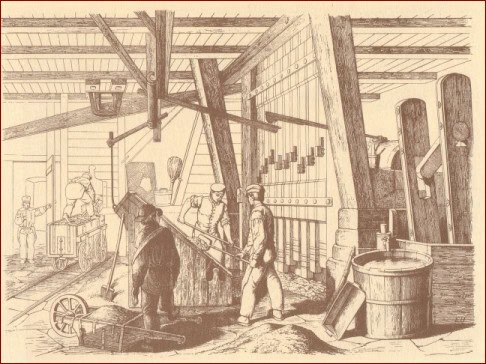
Das zum gleichen Zwecke dienende Walz- oder Quetschwerk zerkleinerte die Erzstückchen durch zwei scharf nebeneinander gehende starke eiserne Walzen. Unter diesen Walzen befanden sich eine Menge Siebe von verschiedener Feinheit, wodurch das Erz fiel.
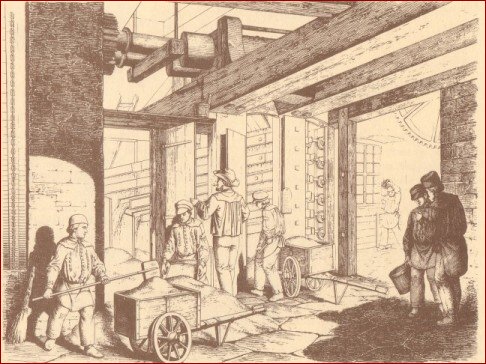
In der letzten Bergbauperiode erfolgte das Zerkleinern des Roherzes in Kugelmühlen. Dabei wurde durch Zugabe von Wasser eine Erztrübe hergestellt. Die Trennung des Erzes und der tauben Bestandteile erfolgte durch Flotation. Dabei wurde durch Zugabe bestimmter Chemikalien die Oberfläche der Erzteilchen wasserabweisend. Durch Einblasen von Luft lagerte sich das Erz an dem entstehenden Schaum ab. Dieser wurde abgestrichen, das taube Material sank in der Flotationszelle zu Boden und wurde abgetragen.